
This material makes the socket head bolts highly resistant to corrosive acids. The cap screws also are made from SUS316/316L steel. SUS hex socket cap screws have 18% chromium and 8% nickel added to the steel for added durability. The SUS designation of the socket cap screws refer to the stainless steel grade of SUS304 the fasteners bearing this designation are manufactured from for high-temperature use, they’re also offered in SUS310S stainless steel. Hexagon socket screws are typically used in applications where the use of standard screws is restricted because the tools used to loosen and tighten the fasteners cannot access the fastener’s location. Hexagon socket screws were developed as a solution to the increasingly smaller tolerances and available space in many of today's manufacturing designs and engineering solutions. designs, engineers, and manufactures hexagon socket head cap screws and SUS socket cap screws to suit every application in machining and metal manufacturing. Not so much because of the bolt strength, but because of the material removed for the countersink.Hanshin Neji (Thailand) Co., Ltd. For something where brute strength is required (like an automotive frame), I would prefer a regular bolt, not countersunk.
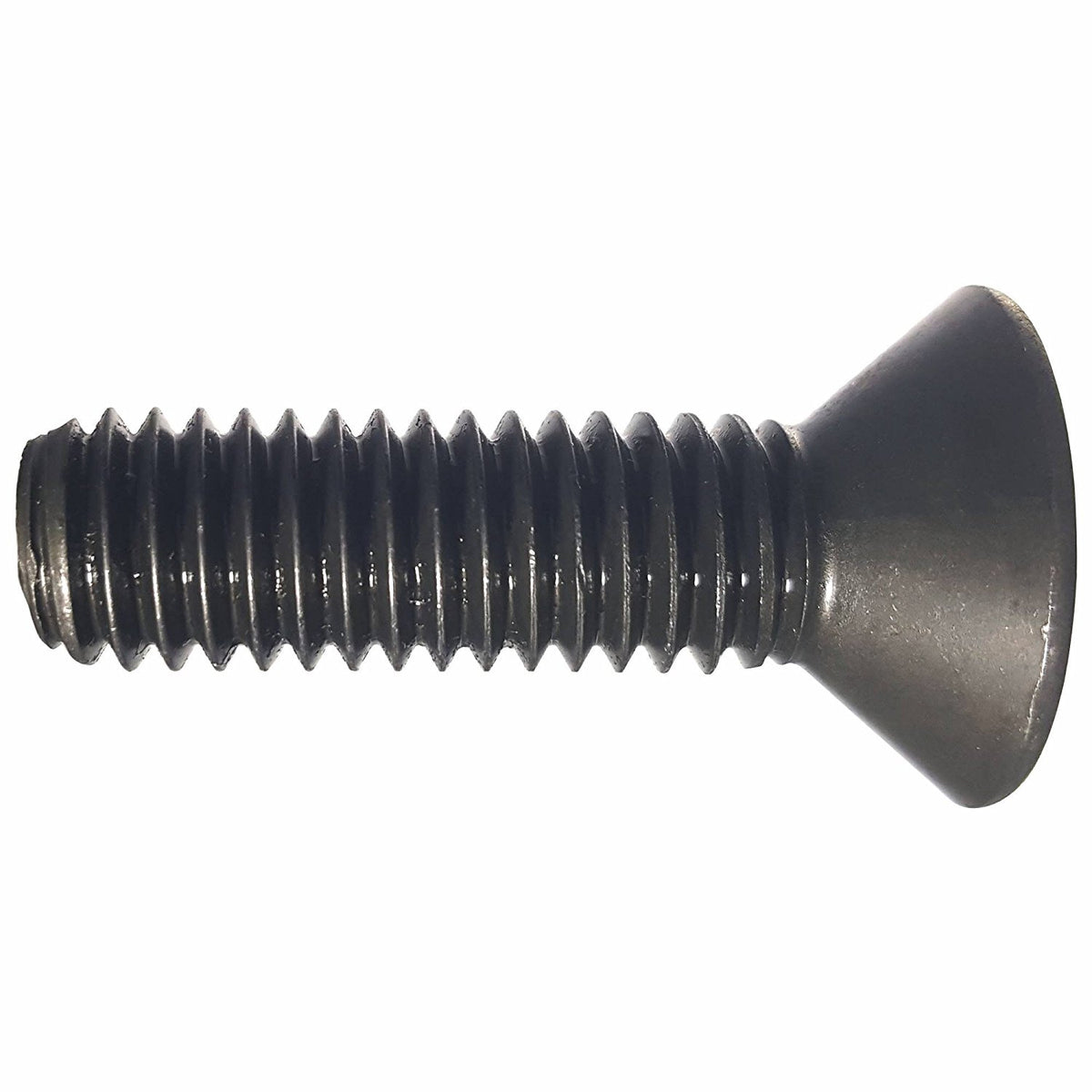
If I need either one of those, I switch to flat heads. Here's how I would choose: If centering or flush installation aren't required, I'd go with a cap screw by default. But if you need it to be flush, drilling a countersink is usually much easier than drilling a counter-bore.Ĭap screws can be installed in slots and flat heads can't (that I know of).

A caps screw above the surface is the simplest mechanically. A cap head screw with an oversized hole can accommodate some misalignment without warping the parts being attached.Īlso adding to something others have mentioned. I find that this is usually an advantage, but it can also be a disadvantage. You can give the screw hole a generous clearance, and when the screw is tightened down, the parts will still be forced into alignment (in the plane perpendicular to the screw). They are self centering when used in a tapped hole.
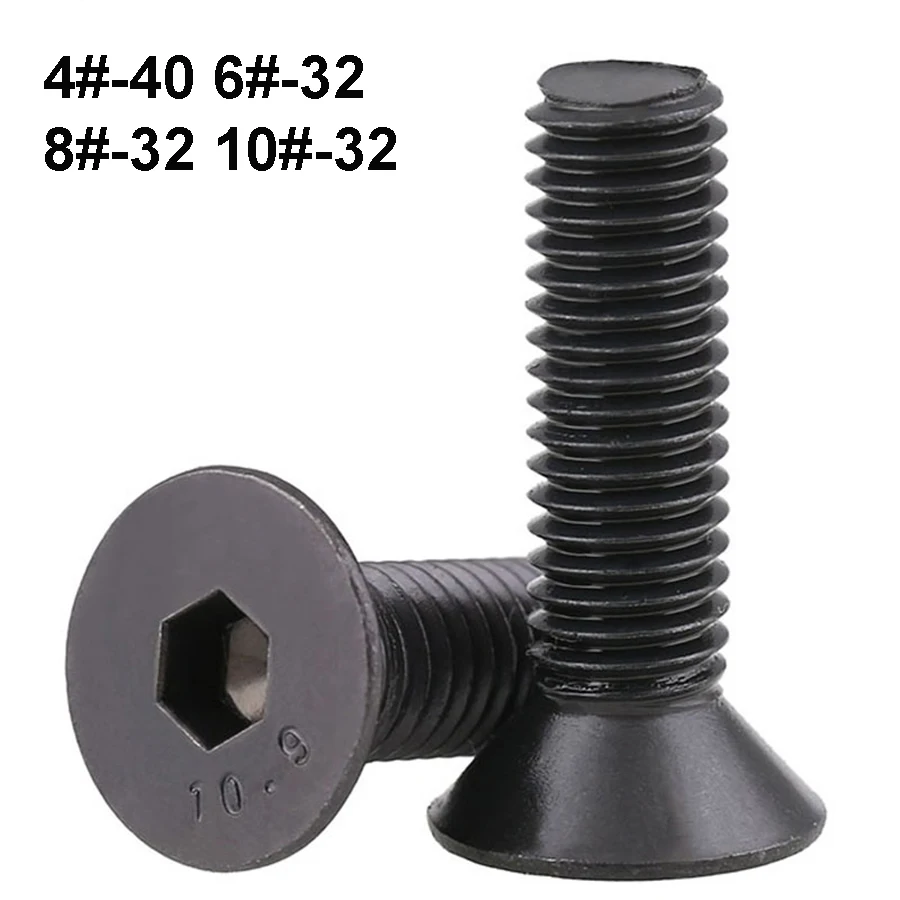
Counter sunk screws have an additional advantage that I haven't seen anyone mention.
